基于现阶段电子芯片的综合性能越来越高、整体尺寸越来越小的发展情况,电子芯片工作过程中所呈现出的热流密度同样大幅提升。因此,选用合适的封装材料与工艺、提高器件散热能力就成为发展功率器件的技术瓶颈。陶瓷材料本身具有热导率高、耐热性好、高绝缘、高强度、与芯片材料热匹配等性能,非常适合作为功率器件封装基板。
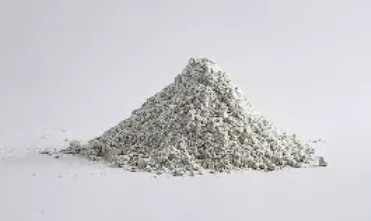
其中,氮化铝是导热性能最为优良的陶瓷材料,其理论热导率可达320W/(m·K),其商用产品热导率一般为180W/(m·K)~260W/(m·K),使其能够用于高功率、高引线和大尺寸芯片封装基板材料。除高导热外,其优良特性还包括:(1)热膨胀系数(4.3×10-6/℃)与半导体硅材料((3.5~4.0)×10-6/℃)匹配;(3)电性能优良,具有极高的绝缘电阻和低的介质损耗;(4)可以进行多层布线,实现封装的高密度和小型化;
因此,氮化铝被认为是新一代散热基板和电子器件封装的理想材料。此外,AlN晶体是GaN、AlGaN以及AlN外延材料的理想衬底。与蓝宝石或SiC衬底相比,AlN与GaN热匹配和化学兼容性更高、衬底与外延层之间的应力更小。因此,AlN晶体作为GaN外延衬底时可大幅度降低器件中的缺陷密度,提高器件的性能,在制备高温、高频、高功率电子器件方面有很好的应用前景。
氮化硅
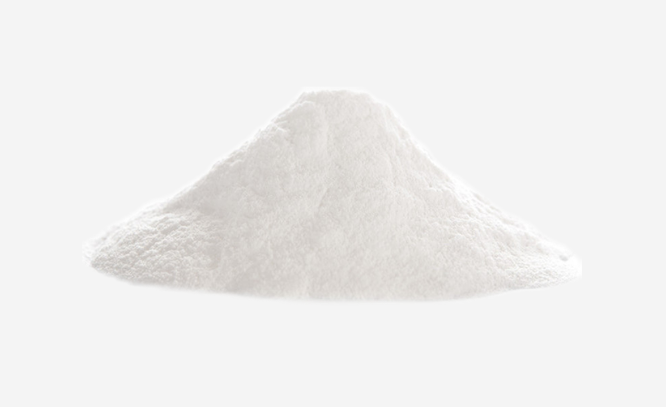
图片来源:青岛瓷兴
氮化硅目前主要用作陶瓷材料,氮化硅陶瓷是工业技术特别是尖端技术中不可缺少的关键材料。例如:在机械领域可用作高速车刀、轴承、发动机刮片、燃气轮机的导向叶片和涡轮叶片等;作为导热、力学综合性能最好的陶瓷材料可用于散热基板;较高的强度和韧性以及优异的化学稳定性和生物相容性使其非常适合作为生物陶瓷;优异的力学性能和热稳定性,较低的介电常数,较好的抗烧蚀性能使其成为最有希望的天线罩材料......目前,氮化硅作为轴承球材料和散热基板材料最受瞩目。其中,轴承球是应用最为广泛的氮化硅陶瓷制品,其年产量占全球高性能氮化硅制品的十分之三。氮化硅陶瓷轴承球与钢质球相比具有突出的优点:密度低、耐高温、自润滑、耐腐蚀、疲劳寿命破坏方式与钢质球相同。因此,氮化硅陶瓷轴承球可广泛应用于机床精密轴承、汽车轴承、风力发电机绝缘轴承、石油化工耐腐蚀和耐高温轴承等领域。
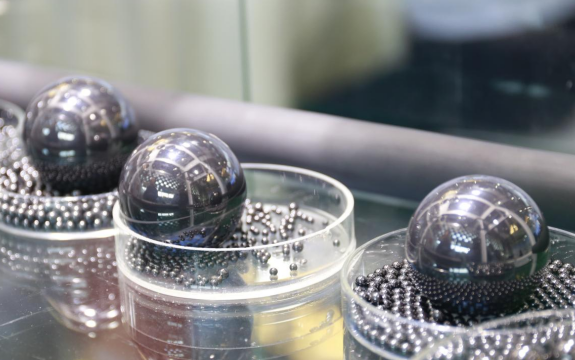
尤其是,氮化硅陶瓷球除这些优异的性能之外还具有良好的绝缘性,能够解决因电腐蚀带来的轴承表面损坏、润滑剂过早老化、产生异响等影响,非常适合应用于电动汽车等领域。在散热基板方面,其理论热导率值最高可达320W/(m·K),科研人员通过工艺优化,氮化硅陶瓷实际使用热导率不断提高,目前已突破177W/(m·K)。此外,氮化硅较AlN具有更高的强度、韧性和硬度。所以高性能氮化硅导热基板材料成为国内外先进陶瓷研究机构和企业争相研制与开发的下一代高性能导热基板材料。
在众多导热粉体材料中,综合性能、技术成熟度、生产成本等,球形氧化铝凭借较高的导热性能、高填充系数、较好的流动性、成熟的工艺、丰富的规格以及相对合理的价格,成为导热粉体行业中高端导热领域最主流的导热粉体类别。
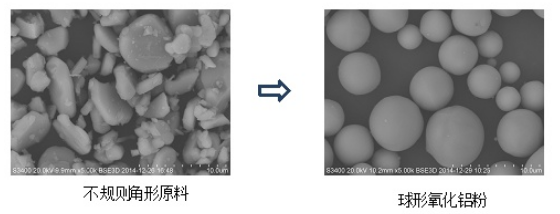
在汽车电动化的浪潮下,国内外主流车企纷纷加大新能源汽车战略布局,新能源汽车进入市场驱动的高速成长期。由于政府的大力支持以及从我国能源供给情况来看,我国新能源汽车市场将保持快速发展的态势。而新能源汽车电池、电控、电机均采用导热材料及导热胶等热界面材料,有望带动球形氧化铝填充料需求。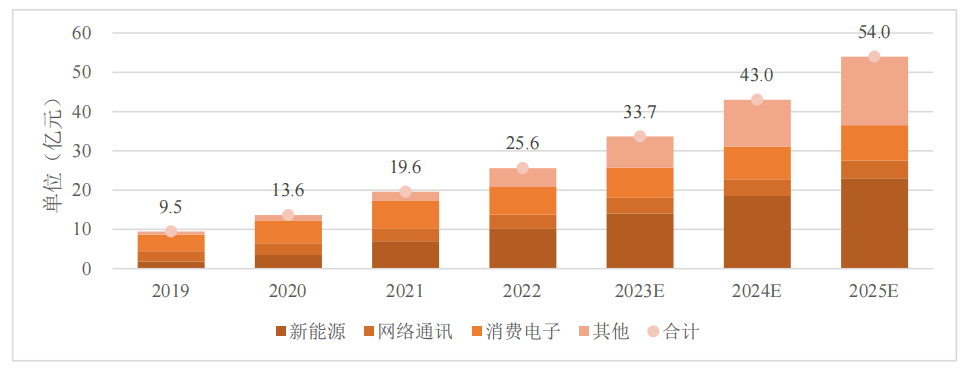
根据高工产业研究院数据,2022年全球导热粉体材料市场规模为50.4亿元,其中球形氧化铝导热粉体市场规模占比50.8%,为25.6亿元,同比增长30.7%。据壹石通公告,单辆新能源汽车大约需要使用不低于10kg的球形氧化铝,而且新能源汽车市场仍在快速增长,再加上氧化铝价格下降使得其在5G、消费电子领域导热粉体材料中渗透率增加。据预测2022-2025年全球球形氧化铝导热材料市场规模年复合增速将达28.2%,到2025年将达54.0亿元。此外,球形的粉体因具有规则的形貌、更大的堆积密度、好的流动性等性质,可大大提高产品的应能。因而,除了在导热领域以外,球形Al2O3粉体在陶瓷、催化剂载体等多个领域被广泛的应用与研究。
钛酸钡(BaTiO3)是一种ABO3型钙钛矿结构,自从20世纪上半叶,钛酸钡陶瓷的优异介电性能被发现,便被用来做电容器的介质材料,它是目前使用最普遍的电子陶瓷粉体之一,还是制造电子元件的母体材料,因此被人们称作“电子陶瓷工业的支柱”。
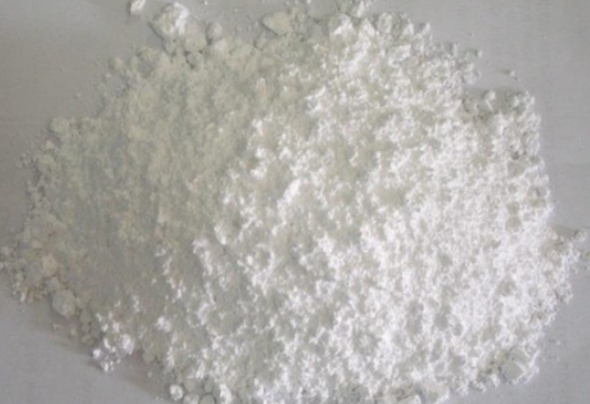
近年来,电子制造业飞速发展,而世界上几乎70%的MLCC被运用在电子产品上。根据中国电子元件行业协会公布数据,2022年中国MLCC行业市场规模约为596亿元,到2026年预计将达726亿元。作为MLCC核心原材料,钛酸钡粉体需求将不断攀升。在国际市场上,钛酸钡粉体生产企业主要有村田、日本住友、杜邦、中央硝子、TDK、日本堺化学等。与国际企业相比,我国钛酸钡粉体企业在技术、规模、产品性能等方面仍存在差距,尤其在高端纳米钛酸钡粉体领域,我国纳米钛酸钡粉体大多从日美等国家采购,价格居高不下,受制于人。另外,微型化的MLCC是后续多层陶瓷电容器发展的主要方向,这主要是因为电子设备逐渐向微型化、薄层化方向发展。在介质层的薄型化方面,日本企业仍处于领先地位,介质层厚度为1μm的多层陶瓷电容器已经量产,研发厚度已达到0.3μm。介质层薄层化的基础是钛酸钡陶瓷粉体的细化,在多层陶瓷电容器介质层厚度越来越小的情况下,为提高元件的稳定性和可靠性,钛酸钡作为多层陶瓷电容器的主要原料,主要使用的钛酸钡粉体的尺寸为80-150nm。因此,高性能钛酸钡粉体材料是实现高性能MLCC国产化的关键。
纳米复合氧化锆是一类加入稳定剂后在室温条件下仍能保持四方相或者立方相的氧化锆,稳定剂主要为稀土氧化物(Y2O3、CeO2等)及碱土金属氧化物(CaO、MgO等)。
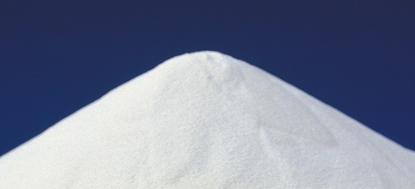
随着科学技术的发展和进步,各种能满足特殊使用条件和使用功能的仪器、设备层出不穷,对材料及部件功能的要求也越来越高,世界市场对兼具高韧性、耐高温、耐磨损、耐腐蚀和特殊光学性能的纳米复合氧化锆材料及其制件的需求增长迅猛。氧化钇稳定氧化锆是应用最广、最具代表性的纳米复合氧化锆,其具有较高的氧离子导电特性、良好的机械性能,耐氧化及耐腐蚀性能、高热膨胀系数、低热导率及良好的抗氧化性和稳定性等优点,被广泛应用于结构材料和功能材料,如氧传感器、氧气泵、高温固体燃料电池、铁电陶瓷及航空发动机涂层等。国内某锆业龙头相关负责人曾向媒体表示,“相比手机背板,业内更看好纳米级复合氧化锆在三元正极材料方面的增量市场空间和齿科生物用材料的市场发展空间。”以齿科为例,据估算,国内每年所需齿科用纳米级氧化锆已超过2000吨,且复合增长率达到10%以上。
碳化硅材料主要可分为陶瓷和单晶两类。作为陶瓷材料,其在一般的应用领域对纯度要求并不是很严格,但在一些特殊环境下,如光刻机等半导体设备中作为精密部件时需对其纯度进行严格控制,以免影响硅片的纯净度。单晶方面,碳化硅(SiC)作为重要的第三代半导体材料之一,在高温、高频、高功率、抗辐射等方面具有优秀的性能。SiC基器件已经在军事、民事、航空航天等多领域得到了广泛应用,是各国科学技术竞争的重点领域。SiC单晶作为SiC产业链的基石有着至关重要的地位。然而,SiC的本身特性决定了其单晶生长难度较大。这主要是由于在常压下没有化学计量比为Si:C=1:1的液相存在,并不能采用目前半导体工业主流所采用的生长工艺较成熟的生长法——直拉法、降坩埚法等方法进行生长。为了克服这一难题,科学家们经过不懈努力提出了各种方法以获得高结晶质量、大尺寸、廉价的SiC晶体。目前比较主流的方法有物理气相传输法(PVT法)、液相法以及高温气相化学沉积法等。其中PVT法是主要的碳化硅单晶制备工艺,在PVT法中,影响SiC晶体合成的因素有很多,其中SiC粉体作为合成原料会直接影响SiC单晶的生长质量和电学性质。有科研人员研究了不同粒径以及不同杂质含量的SiC粉体对SiC单晶生长的影响,发现单晶中大部分的杂质均来自SiC粉体,单晶的质量与粉体的纯度呈线性关系。由于SiC粉体在单晶生长过程中发挥着重要作用,近年来,制备高纯的SiC粉体逐渐成为SiC单晶生长领域的研究热点。目前可以大批量生产高纯SiC粉体的公司有中国的天科合达、法国圣戈班、日本太平洋等,不同公司合成的SiC粉体的纯度不同,价格也不同。据统计,这些SiC粉体的粒径约为300~500μm,纯度(质量分数,下同)在99.95%~99.9999%之间,价格在2000~12000元/kg之间。因此,低成本、高效率的合成高纯碳化硅微粉是第三代半导体产业链备受关注的一环。
参考来源:中国粉体网、粉体的设计研究